A Lithium mine in Western Australia were experiencing a disruptive three week maintenance shut cycle due to severe wear on 6/4DD-AH pumps.
Our client wanted to increase the interval between shuts to at least four weeks. Extending the wear life of this pump and any other item with a 3-week cycle rate, so the site shuts occur every 4 weeks. The site was using a variable speed driven 6/4DD-AH Warman pump, which was fitted with a relatively new design concept marketed as ‘WRT’. Our team conducted wear analysis using laser scanning which showed this impeller design was not only causing unusual wear patterns, but also accelerated wear of the volute liner, throat bush and suction side impeller pump out vanes.
We replaced the ‘WRT’ impeller with a more conventional ‘twisted vane’ impeller design, to extend the expected wear life of the volute liner, the throat bush and the impeller itself, thereby enhancing the overall wear life of the pump. This change has added over A$1,500,000 per annum to the bottom line (see cost variation table).
If you have any questions about how we can help extend pump wear life on your site, contact us or call +61 (08) 9480 0473.
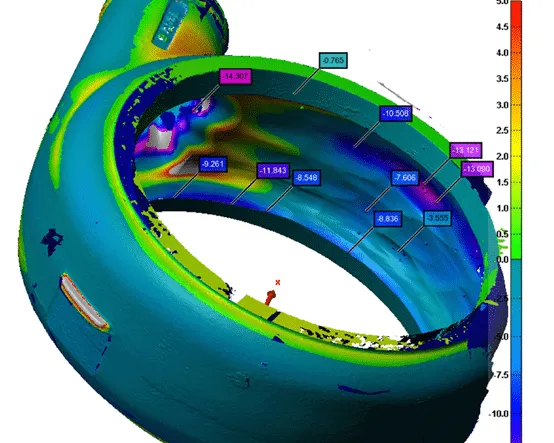
